Fixed electrical sensors are an essential component in various industries, including automotive, aerospace, and manufacturing. These sensors play a crucial role in detecting changes in the environment and converting them into electrical signals for monitoring and control purposes. The production process of fixed electrical sensors involves several steps to ensure their accuracy, reliability, and performance. In this article, we will explore the mainstream production process of fixed electrical sensors.
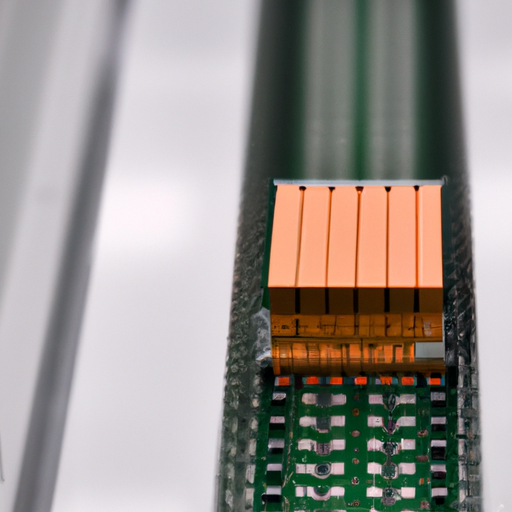
The first step in the production process of fixed electrical sensors is the design and development phase. This phase involves defining the specifications and requirements of the sensor, such as the type of sensor, sensing range, accuracy, and response time. Engineers and designers work together to create a detailed design of the sensor, including the materials, components, and circuitry needed for its operation.
During the design phase, computer-aided design (CAD) software is used to create 3D models of the sensor and simulate its performance under different conditions. This helps identify any potential issues or limitations in the design before moving on to the next phase of production.
2. Material Selection
Once the design is finalized, the next step is to select the materials for the sensor components. The choice of materials is critical to the performance and reliability of the sensor. Common materials used in fixed electrical sensors include metals, ceramics, and polymers, depending on the application requirements.
For example, in high-temperature environments, materials such as stainless steel or ceramic are used for their thermal stability and resistance to corrosion. In contrast, in applications where weight is a concern, lightweight materials like aluminum or plastic may be preferred.
3. Manufacturing
The manufacturing process of fixed electrical sensors involves several steps, including fabrication, assembly, and testing. The fabrication of sensor components is typically done using machining, casting, or molding processes, depending on the complexity and size of the parts.
Once the components are fabricated, they are assembled into the final sensor unit. This involves connecting the sensor elements, circuitry, and housing together to form a complete sensor. The assembly process is done with precision to ensure proper alignment and functionality of the sensor.
4. Calibration and Testing
After the sensor is assembled, it undergoes calibration and testing to verify its performance and accuracy. Calibration involves adjusting the sensor to ensure that it provides accurate measurements within the specified range. This is done using calibration equipment and reference standards to compare the sensor's output with known values.
Testing is also conducted to evaluate the sensor's response time, sensitivity, and reliability under different conditions. This may involve subjecting the sensor to temperature, humidity, and vibration tests to simulate real-world operating conditions. Any issues or deviations from the specifications are identified and addressed during this phase.
5. Quality Control
Quality control is an essential part of the production process to ensure that the sensors meet the required standards and specifications. This involves inspecting the sensor components and assemblies at various stages of production to identify any defects or inconsistencies. Quality control measures may include visual inspection, dimensional checks, and functional testing to verify the sensor's performance.
In addition to in-process quality control, final inspection is also conducted before the sensors are shipped to customers. This involves a thorough evaluation of the sensors to ensure they meet all the specified requirements and are free from defects. Any non-conforming sensors are rejected or reworked to meet the quality standards.
6. Packaging and Shipping
Once the sensors have passed all quality control checks, they are packaged and prepared for shipping to customers. Packaging is done to protect the sensors from damage during transportation and storage. This may involve using protective materials such as foam, bubble wrap, or cardboard boxes to ensure the sensors arrive in good condition.
Shipping methods vary depending on the customer's location and requirements. Sensors may be shipped via air, sea, or land transportation to reach their destination. Proper handling and tracking of the shipment are essential to ensure timely delivery and customer satisfaction.
In conclusion, the production process of fixed electrical sensors involves several critical steps to ensure the sensors meet the required specifications and performance standards. From design and development to manufacturing, calibration, testing, quality control, and shipping, each phase plays a crucial role in producing high-quality sensors for various applications. By following a systematic and rigorous production process, manufacturers can ensure the reliability and accuracy of fixed electrical sensors for use in diverse industries.